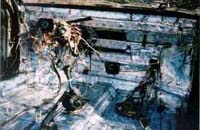 |
Таким образом медленно и печально, оклеивался сначала щиток, потом
тоннель пола, пол. В некоторых местах, а именно: часть передних арок,
небольшую площадь на щитке, и на тоннеле пола, я поклеил вторым слоем
ВП. Незнаю какой процент это внесло в общую картину, скорее всего
небольшой. Как уже упоминал, самая неудобная часть кузова для оклейки,
это щиток со стороны водителя, вот где действительно пришлось попотеть,
архинеудобно. Притом, два раза головой, и два раза коленкой, весьма
ощутимо приложился об выступающую часть привода рулевого управления :)
|